低压铸造液面加压控制系统
CLP—11型智能低压铸造液面加压控制
第一部分 气路控制 |
一、概述 《CLP-11》型低压铸造液面加压控制系统,主要用于对内部组织要求致密的复杂鋳件,它是依据低压铸造原理,在密封的坩埚(保温炉)中,通入干燥的压缩空气,在压力的作用下,坩埚(保温炉)内的液态金属通过升液管压入型腔内,使之在压力下充型、结晶、形成鋳件。特别适宜对气密性要求较高的鋳件。本控制系统是以集成技术生产的,是用气动薄膜调节阀组成的双阀推挽式压力跟踪器为核心的闭环反馈系统,整机结构简单、运行可靠、抗干扰能力强。系统采用计算机控制,用触摸屏作人机界面,可完成的工艺曲线如图(1)所示: |
二、主要技术指标 1)加压速度范围:0~10KPa/s; 2)增压补缩的压力范围:0~100KPa; 3)结壳、增压、保压、开模提示的总延时范围:1s~3600s; 4)抗干扰能力: 1、型腔断面的变化不影响工艺过程; 2、坩埚的漏气量20m/h时不影响工艺过程; 3、气源压力波动在0.4~1MPa的范围内不影响工艺过程。 |
三、结构及工作原理 本计算机用触摸屏作人机界面,由气路和电路两部分构成,各自独立,用几组航空插件相互连接组成,一个闭环反馈控制系统由控制信号发生器、检测坩埚内(炉体)压力的传感器、比较器、放大器、调节器、执行器等部件组成,本系统把它们的连接通道都集成在二块阀柱上。用一个恒压阀稳定外部波动的气源压力。设备设有外界气源压力表"6"(见图2)显示气源压力,系统可存储20套工艺曲线,操作者可按后续说明进行设置、修改、储存使用。 工作原理,预先按要求设置好生产铸件的工艺曲线。推挽式压力跟踪系统跟随控制信号对应的工艺曲线对坩埚(炉体)加压,因采用了闭环控制,当控制信号按一定工艺曲线给定后,控制系统可排除各种干扰,按原给定的工艺参数完成对铸件的浇铸。 |
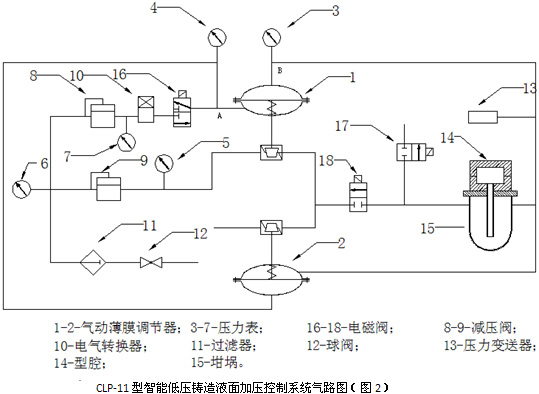
四、系统特点 1)通过计算机软件对系统工况的分析判断本智能低压铸造液面加压控制系统,可自动准确的完成升液转充型、充型转增压的跳转这就可使充满型后立即增压,为及时补缩迎来宝贵的时间,为提高铸件的致密性提供了可能。 2)本系统为快速性较差的比例调节器因而在填充水平放置的轮辐时有缓冲作用,基本上消除了铝液在轮辐内的喷射及飞溅,使在该处不易产生液气两相流 进而为提高轮辋、内轮缘的质量提供了可能。 3)由于升液转充型、充型转结壳(或转增压)的跳转是由计算机自动完成的,因而本控制系统无需设置液位补偿。 4)本系统备有顺序凝固和同时凝固的两种充型加压方式,为进一步提高鋳件的内在质量提供了可能。 5)本计算机控制系统用触摸屏作人机交流界面,因而外观结构简单,使用、维护方便,运行稳定可靠; 6)本控制系统也可采用时间、压力、液位补偿的传统方式控制; 7)本计算机控制系统是两套不同算法的控制软件同时运行,以提高可靠性; 8)本计算机控制系统的软件有容错功能(即控制软件出现失误计算机自行提示并纠正继续完成工艺过程) 9)本控制系统具有电、气双重过压保护及报警功能; 10)本控制系统抗电磁干扰能力强; 11)当控制系统的压力传感器出现故障计算机控制系统自动提示并报警; 12)由于采用了推挽式压力跟踪器控制,从结构上抑制了超调; 13)由于控制系统气动调节部分直接安装在炉体背后,连接管路短故压力跟踪的稳定性进一步提高; |
五、安装与调试 1)把压缩空气气源接入系统的进气端,接入管路前,一定要清理干净,以防杂物进入气路中; 2)系统的输出用软胶管或金属管与坩埚(炉体)连接,管的内径不得小于25mm; 3)将AC220V电源接到系统的电源端子板上; 4)系统的外壳要良好接地; 5)系统压力的设定:外界气源压力应不低于0.4MPa由表"6"指示,调节恒压阀"9、8"(见图2),使压力表"5"指示在0.3MPa,在压力表7指示在0.14Mpa 6)密封好升液管口,直接设置工艺曲线,关闭排气阀17并使炉中液面低于升液管下沿而后准热态运行。 |
六、使用及维护 1)将坩埚和升液管口封好,打开系统和坩埚(炉体)间的阀门"18",关闭阀门"17",对前述设置好的工艺曲线进行试运行,如同前述工艺曲线运行状态一致说明正常,可进行下一步,如果跟踪曲线(绿色)远低于给定曲线(红色),可能是坩埚(炉体)漏气严重,或气源功率不够、管路细长造成的,应排除后继续调试; 2)坩埚(炉体)中倒入液态金属; 3)扒出升液管内液态金属表层的渣物,合型后即可充型; 4)升液转充型计算机自动判断完成; 5)充型转增压计算机自动判断完成; 6)系统的进气端要加冷干机,以保证进入坩埚内(炉体)的气体干燥、洁净。过滤器中的污水及赃物要勤排放清理; 7)停机后必须关掉电源和气源。 |
第二部分 电器控制 |
一、特点 《CLP-11》型低压鋳造液面加压控制系统,采用计算机控制,可实现工艺参数的设定、显示,并且可将20种不同类型的工艺参数预置在计算机的存储器内,需要时可任意选取。图(6、7)为电器原理图及布线图 。 |
二、《CLP-11》型智能低压铸造液面加压控制系统操作面板说明 1)CMP—触摸屏,使用方法详见随机文件; 2)SB1—控制电源按钮(HL1-上电指示灯,附在控制电源按钮上); 3)SB2—启动按钮(HL2-启动指示灯,附在启动按钮上); 4)SB3—手动翻转按钮(HL3-手动翻转指示灯,附在手动翻转按钮上); 5)SB4—紧急排气按钮(HL4-紧急排气指示灯,附在紧急排气按钮上); 6)AH—故障报警指示灯。 |
三、系统调试 关闭系统与坩埚(炉体)间的阀门"18"(见图2),合上断路器"QF",打开"控制电源"开关SB1,则"控制电源"指示灯亮HL1亮,触摸屏上电,彩屏显示见图(3): |
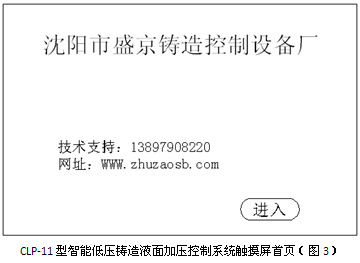
点击"进入",彩屏显示"控制"界面,见图(4):图中右侧有五个按钮:"启动"、"手动翻转"、"紧急排气"按钮和控制柜的操作面板上相同名称的三个按钮作用相同(详见图8)。按"退出"按钮,彩屏返回首页界面。
如在控制界面按"设置"按钮,彩屏显示"功能设置界面",见图(5)。如"工艺1"参数的设置:常规参数值如图(5)所示,为保证自动翻转的时间、压力均在小于设定值之前完成,必须使设定值在保持升压速率不变的前提下,均提高20%左右,即:升液压力41KPa;、升液时间58S(升液时常规压力取值应不低于压铸最后一铸件时液态金属升到升液管口的压力值,调节升液、充型时间,改变升液、充型速率)、充型压力到60KPa、充型时间48S;充型结束时的压力为结壳压力,结壳时间对于砂型铸造可根据铸件的形状、大小设置;对于金属型铸造,一般设为0,则跳过结壳,直接转为增压。由于增压开始以后计算机没有自动翻转的任务,因而增压压力值和增压耗用时间及保压延时可按原常规工艺去给定,例如:增压压力到65KPa,增压延时3S。保压压力65KPa,保压时间100S。最后剩"自动功能"设置项,用手指触碰右面小键盘上面的"0"为停用;当触碰非"0"的任意数码时,都显示自动功能启动。如图5所示,以上数据键入后,再按"确定"键,工艺参数设置完成。在按"退出"键,彩屏转回控制界面。密封好升液管口,打开系统与坩埚(炉体)间的阀门,再用上述工艺参数运行几次,如没问题,即可投入使用了。
四、系统特点 1)通过计算机软件对系统工况的分析判断本智能低压铸造液面加压控制系统,可自动准确的完成升液转充型、充型转增压的跳转这就可使充满型后立即增压,为及时补缩迎来宝贵的时间,为提高铸件的致密性提供了可能。 2)本系统为快速性较差的比例调节器因而在填充水平放置的轮辐时有缓冲作用,基本上消除了铝液在轮辐内的喷射及飞溅,使在该处不易产生液气两相流 进而为提高轮辋、内轮缘的质量提供了可能。 3)由于升液转充型、充型转结壳(或转增压)的跳转是由计算机自动完成的,因而本控制系统无需设置液位补偿。 4)本系统备有顺序凝固和同时凝固的两种充型加压方式,为进一步提高鋳件的内在质量提供了可能。 5)本计算机控制系统用触摸屏作人机交流界面,因而外观结构简单,使用、维护方便,运行稳定可靠; 6)本控制系统也可采用时间、压力、液位补偿的传统方式控制; 7)本计算机控制系统是两套不同算法的控制软件同时运行,以提高可靠性; 8)本计算机控制系统的软件有容错功能(即控制软件出现失误计算机自行提示并纠正继续完成工艺过程) 9)本控制系统具有电、气双重过压保护及报警功能; 10)本控制系统抗电磁干扰能力强; 11)当控制系统的压力传感器出现故障计算机控制系统自动提示并报警; 12)由于采用了推挽式压力跟踪器控制,从结构上抑制了超调; 13)由于控制系统气动调节部分直接安装在炉体背后,连接管路短故压力跟踪的稳定性进一步提高; |
五、安装与调试 1)把压缩空气气源接入系统的进气端,接入管路前,一定要清理干净,以防杂物进入气路中; 2)系统的输出用软胶管或金属管与坩埚(炉体)连接,管的内径不得小于25mm; 3)将AC220V电源接到系统的电源端子板上; 4)系统的外壳要良好接地; 5)系统压力的设定:外界气源压力应不低于0.4MPa由表"6"指示,调节恒压阀"9、8"(见图2),使压力表"5"指示在0.3MPa,在压力表7指示在0.14Mpa 6)密封好升液管口,直接设置工艺曲线,关闭排气阀17并使炉中液面低于升液管下沿而后准热态运行。 |
六、使用及维护 1)将坩埚和升液管口封好,打开系统和坩埚(炉体)间的阀门"18",关闭阀门"17",对前述设置好的工艺曲线进行试运行,如同前述工艺曲线运行状态一致说明正常,可进行下一步,如果跟踪曲线(绿色)远低于给定曲线(红色),可能是坩埚(炉体)漏气严重,或气源功率不够、管路细长造成的,应排除后继续调试; 2)坩埚(炉体)中倒入液态金属; 3)扒出升液管内液态金属表层的渣物,合型后即可充型; 4)升液转充型计算机自动判断完成; 5)充型转增压计算机自动判断完成; 6)系统的进气端要加冷干机,以保证进入坩埚内(炉体)的气体干燥、洁净。过滤器中的污水及赃物要勤排放清理; 7)停机后必须关掉电源和气源。 |